‘Murphy Pipe and Civil (MPC) Group needed a better way to manage scheduled servicing and retrieval of data from off site locations.Using a paper-based system, the data being retrieved from sites was inconsistent in legibility and missed answers to the key, important questions. We had no way to understand who had previously tended to the plant or equipment, or what actions had been taken or assessments made’.
MPC Group currently has 800+ pieces of maintainable equipment that is spread and distributed across multiple sites throughout Australia.
The servicing and scheduling of defective maintenance and preventative maintenance was a process that was made up of complex spreadsheets and numerous administrative tasks and actions to maintain and ensure they were kept up-to-date.
Corresponding data retrieved from services and maintenance was completed on paper, and then they had to be digitized by an administration team member.
The paper-based system meant that the data that was retrieved from sites was inconsistent in legibility and sometimes missed important information with no ability for mechanics to understand who had previously tended to the plant or equipment.
The latency of these processes put a strain on the scheduling of works, not allowing significant time to plan and still maintain ad hoc priority servicing requirements. As a result of this, the decision was made to find a better way to manage scheduled servicing and retrieval from site.
The Mobile Quality Management System Software was used for MPC Group to replace the pre-start forms for all field based plant and equipment, with the implementation tapered towards the more pressing needs of a system to to meet the wider plant department’s needs.
“The biggest advantage a Quality Management System has to us is having the machinery and vehicle maintenance history at our finger-tips, this is critical for a maintenance department”, Dave Waters - Plant Supervisor, GFS Project
The implementation process was a smooth transition, from paper to glass. The Kontrol4 teams experience in the civil and earthmoving industry made achieving key system outcomes for our business easier than expected, and their enthusiasm to extend themselves to meet our needs was evident.
Implementing the system has allowed MPC Group to ensure its plant and equipment is well maintained, it adds increased accountability, reduces the likelihood of serious incidents or injury and minimizes any unplanned downtime.
This improved reliability allows us to be more productive which translates to better service of our clients.
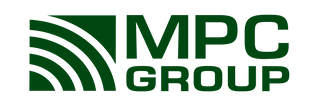